Le rogamos que copie e imprima aquí el manual operativo correspondiente en su idioma. Francais Copiez et imprimez ici la notice d’utilisation dans la langue. SERVICE MANUALScrew Compressor Model: SX 6 classic No.: 9__00USE Contents. KAESER SX6 COMPRESSOR MANUAL SMVLPIMPCZ | PDF | | 24 Aug, TABLE OF KAESER SX6 COMPRESSOR MANUAL.
Kaeser Compressor Sigma Control Manual. Atlas Copco Ga+Xa Technical Kit List 2009. Basic function: ON/OFF. Traffic light functions. Preselect functions. KAESER FILTER products feature a corrosion-resistant steel housing and a stable filter element. Threaded rods and positioning guides ensure rapid element replacement and reliable sealing of filter elements. KB and KE coales-cence filters are equipped as standard with the electronic, level-actuated ECO-DRAIN 31 F Vario condensate drain.
Author: | Merg JoJor |
Country: | Ukraine |
Language: | English (Spanish) |
Genre: | Education |
Published (Last): | 26 June 2009 |
Pages: | 74 |
PDF File Size: | 12.74 Mb |
ePub File Size: | 4.6 Mb |
ISBN: | 443-3-11786-545-6 |
Downloads: | 37762 |
Price: | Free* [*Free Regsitration Required] |
Uploader: | Bralkree |
Make sure you give the data from the nameplate. Consult manufacturer for any other specific power supply.
KAESER SX6 Service Manual
The lubricant also absorbs much of the heat of compression to cool the airend and reduce the temperature of the compressed air. Drive motor terminal box and overload protection relay.
Check tension after the new belts have been in operation for 24 hours. This indicates important information. Safety relief valve blows off Possible cause: Open the shut off valve 10 in the venting line. These conditions are detrimental to correct air treatment.
Coupling defective or Vbelt broken. Main disconnect locked off. External source of compressed air available. Provide adequate compressor ventilation.
Downloads – KAESER KOMPRESSOREN
Check pressure differential and replace oil separator cartridge if necessary. Service work Interval up to hours Check valves. Wear long sleeve garments not synthetics such as polyester and protective gloves. Safety relief valve has blown off.
Other power supplies are not suitable. Activity Danger zone Authorized personnel Transport 10 ft radius from the machine Installation or transport personnel. Carry out a visual check for leaks. Kaeder all air and electrical connections. Drive motor overload protection relay located in the control cabinet.
Check the diaphragm in the vent valve and replace if defective.
Frozen moisture can damage components, diaphragms, valevs and gaskets. They feature excellent lubricity, outstanding demulsibility ability to separate from waterand long life. The compressor motor runs without load and draws little current. Tighten coupling or replace as needed.
Compressed air can cause injury or death. The compresor motor is stopped. Install the new set of belts and use the adhusting nut 1 to adjust tension until the indicator pin 3 reaches the lower end of the elongated hole. Clean or replace clogged parts as necessary.
Before Every Initial Startup Oaeser start up of the machine may only be carried out by trained and authorized installation or maintenance personnel. Changing the cooling oil, oil cooler. Operating in a compressed air system.
Danger of explosion from oils and lubricants! Drain old oil completely and replace with recommended type. Manua inlet valve to maintain adequate idle pressure. Oil leaks out of air filter. Maintenance Within the machine. Clean with compressed air, water or steam injector.
The center of gravity is shown in the drawing in chapter Situate unit for adequate air flow. Contamination of food products when they are processed using unsuitable compressed air. Machine fully vented no pressure.
Kaeser SX-6 Rotary Screw Air Compressor 5HP
Open kaseer shut off valve between the compressor and the compressed air system. Socket is still in the hose coupling at the oil separator tank or aftercooler. Parts contaminated with cooling oil must be disposed of in accordance with local environment protection regulations.
Close off all openings. The aftercooler brings down the compressed air temperature to 5 to 10 K above ambient. Scavenger line is clogged.
Manuals – Manuales – Notices d’utilisation – Bedienungsanleitungen
kaeder WARNING Compressed air and devices under pressure can injure or cause death if the contained energy of the air is released suddenly or uncontrolled. If cooling air outlet duct is used it may be too narrow or too long. Clean the sealing faces. Carefully loosen the fixings 3 and remove the mounting frame. Cooling oil Oil catchment container Thoroughly blow out all the oil from the separator tank and cooler.
TOP 10 Related
Kaeser As25t Manual
Standard Equipment Includes:
Compressor: Single stage, flooded, rotary screw airend with the power saving, proprietary SIGMA profile.
Motor: TEFC electric motor, 1-Phase, 60 Hz., 208 ~ 230., 3,600 rpm, class F insulation, 1.15 service factor and EPAct compliant. Other voltages are available upon request.
Starter: Magnetic wye-delta reduced voltage starter ensures low starting current and soft start.
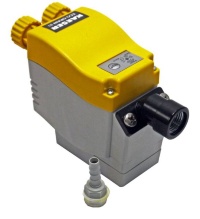
Drive: Maintenance-free elastic belt doesn’t require re-tensioning and maintains efficient power transfer from motor to the airend.
Kaeser Eco Control Basic Manual User
Control Panel: Sigma Control Basic: PLC-based control system with monitoring of emergency stop, motor overload, direction of rotation, airend discharge temperature, refrigerated dryer, analog inputs, cabinet temperature, service hours, back pressure, and minimum starting temperature.Sigma Control Basic ensures economic operation by means of the optimized start-stop control system. This allows the unit to run either fully loaded or off-line to reduce power requirements.
Protective Devices: Built-in protective devices include safety pressure relief valve, emergency stop button, and fluid level sight glasses
Refrigerated Dryer: Single hook up integrated dryer; CFC free R134a refrigerant; 38 deg. F. pressure dew point; stainless steel plate type heat exchanger; moisture separator and Eco-drain. Complete piped internally and ready for installation
Air/Coolant System: Cooling air enters the package though a replaceable and cleanable package pre-filter. A solid steel floor ensures that cooling air must pass through the pre-filter. 4 micron air intake filter replaceable, cleanable cartridge extends fluid drain intervals and air end life. Pneumatic inlet and vent valve. Combined reservoir and separator tank with 3-stage separation system ensures minimal fluid carry over of 1 to 3 ppm (by weight). Quick change devices on the separator and cooler allow complete, fast and easy fluid changes. ASME separator tank is equipped with quick disconnect fittings for manual verification of separator element contamination. Combination valve incorporates a thermostatically controlled valve, cooler by-pass and micro fluid filter. The thermostatically controlled valve ensures perfect regulation of the fluid temperature. The micro fluid filter utilizes a spin-on cartridge. Main fluid and compressed air lines are rigid pipe and incorporate flexible pipe connection. Units are air cooled with high efficiency coolers. Internal fan provides intensive cooling.
Enclosure: Compact unit is soundproofed by a rotation molded double walled, polyethylene enclosure. Compressor is mounted on base frame with a solid steel floor and vibration isolation mounts. Additional vibration isolation for airend, motor, and separator tank is standard. All maintenance and service items are easily accessible once the unit’s removable enclosure is easily lifted away. The electronic condensate drain can be inspected through a pop-out window that also provides access to the condensate drain test button.
Air Receiver: Internally powder coated, includes an electronically controlled condensate drain.
Devices for Ease of Maintenance: Enclosure comes off for easy access for all filter and fluid exchanges; fluid change pressurization valve complete with drain hose; filter mat removal without tools; long life fluid filter.
Warranty: Original KAESER SIGMA air end, electric drive motor and Sigma Control are warranted for a period of two years against defects in materials and workmanship. The balance of the components is warranted for one year.
Optional Five Year Extended Warranty Program: KAESER will extend warranty coverage for 5 years on the airend, motor and Sigma Control (Parts & Labor). All components not specified in the above description are subject to the terms of KAESERS standard warranty policy. To qualify for the extended warranty, a customer must purchase one “5 year Warranty Maintenance Kit” at the time of the compressor purchase and one “5 year Warranty Maintenance Kit” each year of the term of the extended warranty. These new kits include maintenance parts and fluid required for a machine running in a one shift environment. Machines running more than one shift will require additional parts and fluid. Replacement parts and fluid must be genuine KAESER parts. The kits include micro-fiberglass oil filters which are a requirement for the Extended Warranty Program. The fluid included with the kits is S460 Synthetic Lubricant or FG460 Food Grade Lubricant. After the initial fill is removed from the compressor, the compressor must run S460 or FG460 for the life of the Extended Warranty Program. We have a free Lubricant Analysis Program as a required part of the Extended Warranty Program. Recommendations of the Lubricant Analysis Program will supersede the instruction manual.